All Power Labs Gasification and Fischer Tropsch
(2009 - 2012)
All Power Labs started out as a shared artist machine shop and community known as the Shipyard. What started as a Burning Man project has since turned into the renewable energy company APL. The primary focus of the research and product development is the hardware to use gasification of biomass to generate electricity on the scale of 10-20kW (now also a 100kW system). Gasification is generally used to describe the entire process of dehydration, pyrolosis (making char), oxidation/combustion and gasification. Technically gasification is the process of stripping hydrogen and carbon monoxide from charcoal (after the char has been generated). These two "syngases" can then be combusted in an engine and the shaft-power can be used as necessary. Unfortunately, while this gas combination acts very much like propane, it cannot be compressed for storage. Other topics of research to manage this storage issue are catalyst reactions to convert this syngas into a liquid fuel such as diesel - the Fischer Tropsch process is one such method.
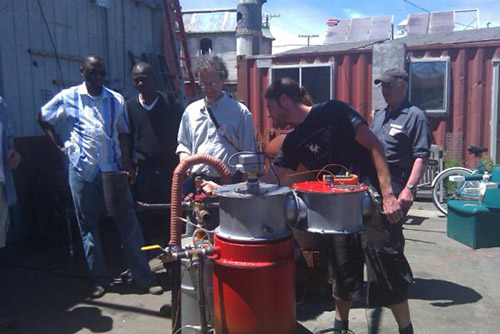
The primary products at APL are the Gasifier Experimenters Kit and the Power Pallet - a 10-20kW gasifier and generator system, shown in the second image. The GEK has shipped to over a hundred countries and consists of just the reduction bell and related hardware to run the pyrolosis and gasification processes, users install their own engines. The Power Pallet system has been shipped to dozens of countries around the world and is essentially a turnkey power generation system, ideal for remote villages.
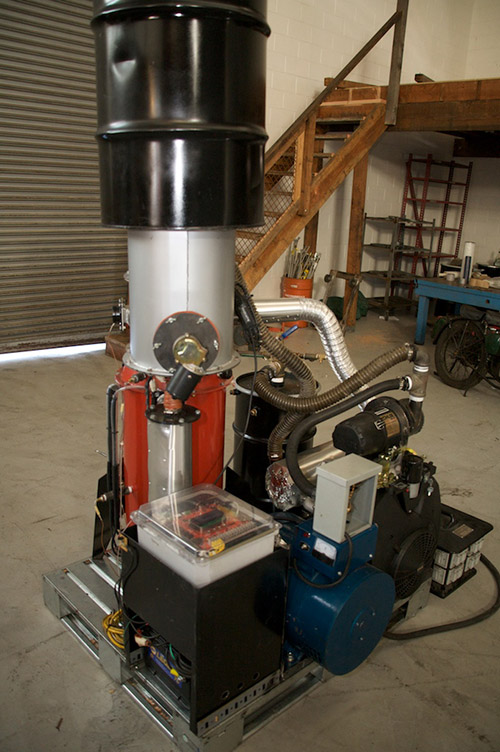
I have been involved in various parts of the projects over the years. Work has included engineering consulting on hardware development such as seals and structure and assembly of both mechanical and electrical systems. I have also been involved in training customers during quarterly hands-on workshops to teach assembly and use of the system (top image). Additional work as included intensive CAD training of APL scientists to help bring the whole system into the 3D design environment.
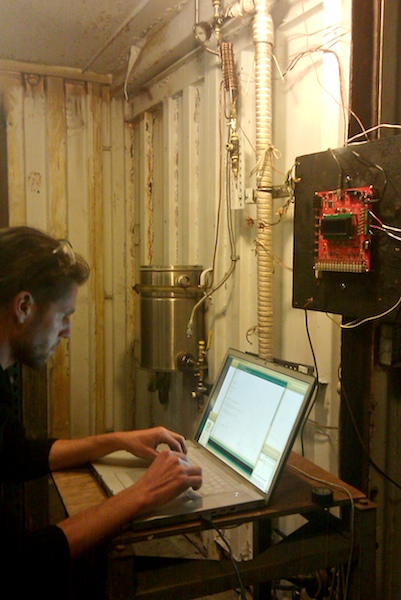
Finally, I was also deeply involved in the development of a small Fischer Tropsch catalyst reactor. This system uses iron-oxide as a catalyst, the exothermic process runs at 300C and 250psi. I calculated heat transfer requirements to verify heating/cooling system specifications. Additionally, I did much of the wiring and coding for the temperature control system; the system runs on a custom arduino “Process Control Unit,” made by APL and visible in the last picture.